Five Effective Ways to Close Manufacturing Labor Gaps
By Adam Grabowski
Director of Marketing, Global Shop Solutions
It has been five years since the COVID pandemic dealt its blow to the manufacturing industry, with 1.4 million workers finding themselves out of a job. Since then the industry has recouped about 800,000 workers, yet the labor shortage continues unabated. It is estimated that four million manufacturing employees will be needed by 2030, but without better recruitment, the industry may fall short by 2.1 million workers.
Fortunately, there are many effective ways to recruit and hire quality employees. They start with knowing what workers want and expect in a manufacturing career. Their expectations can vary to a great degree. However, the following preferences can be found at the top of most manufacturing workers’ priority lists:
Offer a hybrid work model that allows some degree of working outside the office, especially for those with advanced degrees and high-level digital and technical skills.
Cater to younger generation workers who grew up using technology and digital tools in most aspects of their lives. Don’t expect them to seek employment where such an environment isn’t available.
1. Recruit to Your Target
There’s a lot more to recruiting than the standard career web pages, social media advertising, speaking engagements, etc. These five techniques generally produce good results with younger generations and highly educated recruits:
Use Generative AI in Your Recruiting
Generative AI can get results by gathering data and writing the following hiring tasks:
• Create compelling job descriptions for open positions and post them quickly
• Include a chatbot on your career site to answer questions and prompt potential workers to apply for jobs that fit their skills
• Source a large pool of diverse, qualified talent
• Make a list of best-fit candidates to avoid excessive outreach
• Send personalized texts and emails to high-potential candidates
• Send personalized job offer letters to speed up hiring of top talent
Upskilling
Invest in recruiting time with your existing workforce. Upskilling helps retain employees and prepare new employees by developing their skills with new internal training programs.
Promote Manufacturing Careers To Younger Students
Meet with young workers to dispel the misconceptions they hold about manufacturing, such as “long hours, dangerous work and low pay.” Partner with middle and high schools to recruit young workers with training opportunities that teach skills needed for a manufacturing career.
Form Hands-on Training Partnerships for Adults
Partner with community colleges and vocational schools to provide adult students with access to career options they may not be aware of. Look for educational institutions that develop courses to teach the skills in high demand.
Reward for Retention
Recognize and reward employees who follow safety rules, meet their goals and are interested in learning. Create a flexible reward system that gives employees the freedom to choose a reward/incentive they prefer, such as:
• Flexible scheduling, including four-day workweeks and the ability to switch shifts
• Financial incentives like bonuses and profit-sharing
• Paid time off
• Smaller rewards such as weekly lunches when targets are achieved
2. Build a Culture and Environment Where People Want to Work
Make your workforce diverse. Diversity promotes a more dynamic and creative environment that improves employee morale, enhances retention and attracts women, veterans and others seeking a career in manufacturing.
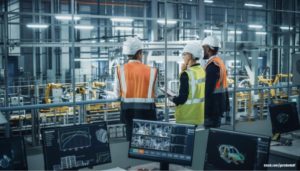
Provide More Opportunities for Women
Many universities are providing technical and digital skills programs for college and high school women. Other programs, such as Manufacturing Institute’s 35×30 campaign, are working to build a more diverse workforce by inspiring and empowering women through recognition, research and leadership.
Look for Military Experience
Reach out to the military community for their discipline, teamwork, leadership and problem-solving skills. Get involved in career fairs and virtual hiring events to learn about attracting, hiring and retaining military talent. Heroes MAKE America is committed to helping manufacturers integrate great talent from the military community into their workforce.
3. Take Care of Your People and They Will Stay
Taking good care of your people and the environment they work in minimizes the need to constantly recruit and hire replacement employees. Valuing your workers motivates them to continue their careers at your place of employment.
• Maintain a safe and positive work environment
• Recognize employees for their efforts and results
• Ask for and listen to employee feedback
• Provide fair compensation and benefits
• Encourage strong peer relationships
• Invest in career growth and development
• Involve employees in your company’s success
Use ERP to automate routine and repetitive tasks, thereby reducing the administrative burden on employees. Offer internships and apprenticeships as a head start to career growth. Encourage studies in fields such as science, technology, engineering and math (STEM) that are critical to manufacturing’s future.
Leverage technology for high-skill workers, such as remote engineers, who can use dashboards and manufacturing apps to provide constant visibility into production from remote locations. With these tools, remote engineers can monitor machines and lines to identify issues and collaborate with on-site colleagues in real-time.
4. Improve Efficiency with ERP Software
Maximizing efficiency can fill some of the labor gaps by providing multiple ways to simplify work processes and work more efficiently.
Using ERP to automate manual tasks provides speed and efficiency in back offices and on the shop floor. It enables employees to complete jobs faster and with greater accuracy, allowing companies to get more done with fewer people. For example, connecting ERP with third-party software like BOM Compare, CAD Interface and Nesting Interface to dramatically reduce the time and manpower needed to build a complex bill of materials, efficiently cut metal from one piece for different jobs and eliminate manual data entry by importing the bill of material into your ERP straight from your CAD software.
Implementing cycle monitoring time measures the efficiency of your production processes using a three-step process to gather data, simplify production processes and optimize people, machines and design. ERP plays a key role in this efficiency technique by tracking real-time data essential to revising and upgrading your processes. When workers are involved in continually simplifying and improving production, it makes them want to be a part of the company.
Make all employees part of your company’s continuous improvement. Engaging staff members in making processes better taps into their personal knowledge base and encourages them to put their ideas into practice. It also helps with employee retention as workers feel they are making a contribution to their jobs and the business as a whole.
Organizing training tailored to the skill sets of individual workers is a good way to attract new employees and upskill existing ones. It is especially good at further developing skills and tasks employees are good at but still have room for improvement. Investing in employee training will cultivate a skilled and loyal workforce for your business.
And finally, implementing paperless manufacturing solutions produces monumental improvements in productivity and efficiency. ERP makes it easy to eliminate or minimize paper usage with barcoding, mobile technologies, tailored dashboards and real-time tracking of labor hours, job costs, defective parts and much more. Switching from paper to digital data recording boosts employee morale to a great degree. Mentioning your paperless environment can also catch the attention of digital job seekers.
5. Emerging Workforce Solutions
Finding skilled workers is challenging, but one emerging solution is hiring outsourced specialists to fill key roles temporarily or on demand.
For example, during and after the COVID pandemic many manufacturers lost their controllers, making it difficult to create accurate financial reports and close the month-end books on time. Manufacturers can now hire experienced controllers to complete the financials every month on a temporary basis. This gives the company time to recruit and hire a full-time financial professional with highly developed financial and ERP skills.
In some manufacturing jobs, it’s okay to start with on-the-job training, but not for jobs requiring advanced degrees. ERP software can help companies track the training requirements, certifications and skills-level of employees to identify gaps that can be closed through training programs and upskilling. If new employees will use ERP on the job, be sure the advanced classes integrate ERP learning with the topic being studied.
The best way to do more with less is to use your ERP system to its full capacity to optimize your people and machines. Start by onboarding or developing an internal ERP “guru” who thoroughly knows your ERP system and can help any user with a problem. Then develop departmental gurus, experienced employees who are trained in the specific areas they use the software for. Create a work environment of continued personal growth and development and you’ll attract employees who want to make working in your manufacturing business a career.
ABOUT THE AUTHOR
Adam Grabowski is the Director of Marketing at Global Shop Solutions. He is responsible for translating the company’s business objectives into successful brand, marketing, and communication strategies to drive awareness, revenue, and loyalty. We simplify your manufacturing. To learn more about Global Shop Solutions, visit www.globalshopsolutions.com.