ZAHORANSKY’S New Micro-Injection Mold for Toothbrush Tips
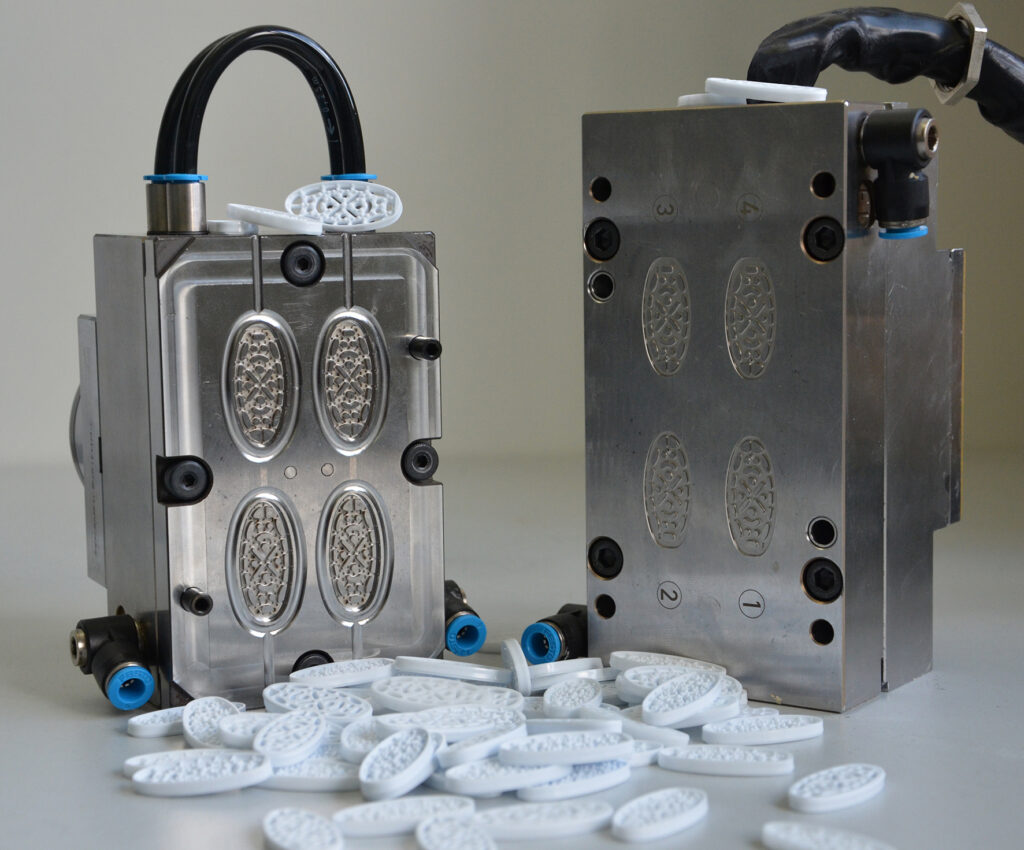
When developing new machines and systems, ZAHORANSKY AG always aims to consistently optimize its production process. In doing so, both economic aspects and the production environment itself are considered equally. With its Micro-Injection Molding Machine, ZAHORANSKY now offers the ideal addition to the Z.VAMP — the specialist machine for toothbrush production which uses the 3D-TUFTING process. The compact Micro Mold from ZAHORANSKY can be placed directly next to the Z.VAMP in combination with a Micro-Injection Molding Machine, and produce the plastic head plates required for toothbrush production on site.
The Micro-Injection Molding Machine requires a minimum space of just under one square meter and can therefore be easily integrated into existing production environments. The head plate output is matched to the performance of the Z.VAMP, perfectly integrating the injection molding and production processes. A further advantage of the new micro-injection molding machine: the on-site and “just-in-time” production of the head plates reduces storage and possible transport costs.
Customization Options Thanks to the Suction Process Method
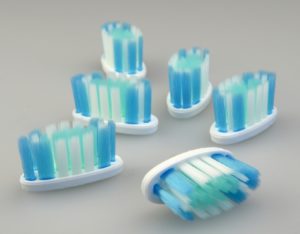
The Z.VAMP is the ideal choice to produce toothbrushes with rigid design requirements for the filament, as it offers maximum customization options in terms of colors, shapes and radii. For example, the angle of the bundles (up to 12 degrees) and filament topography can be selected almost entirely. During the 3D-tufting process, the Z.VAMP fills plastic plates without metal anchors with up to 20,000 monofilaments in just one operation. The filaments, which are rounded in advance, are filled into the head plate via a suction process in freely configurable bundle sizes and then welded at the back. After the assembly and fixation of the equipped head plates in the body of the toothbrush, both parts are welded using ultrasonic technology.
ZAHORANSKY’s 3D-tufting process particularly shows its advantages in the production of toothbrushes with a full set of chemically sharpened filaments. Unlike conventional tamping technology, no scrap is present and no reworking is necessary due to offset filaments. This saves personnel costs, reduces waste, increases productivity and lowers production costs. In addition, hybrid brushes that combine chemically sharpened and standard filaments can also be produced in just one process using the Z.VAMP. As a further example: when combining high and low bundles, the high-quality pre-rounding process achieves a filament rounding quality of up to 98 percent.
To learn more about ZAHORANSKY, visit www.zahoransky.com.