WOMAtec Retrofit Doubles the Lifetime of Used Machines
Daniel Köhler during the startup of his WOMAtec CNC brush control.
Sustainability in Practice with WOMAtec
The hot topic of 2019: Sustainability. Everyone’s talking about it. Although much is discussed and published on the topic, the trend toward the throwaway society continues to grow. Daniel Köhler, Managing Director and owner of WOMAtec Maschinenbau GmbH, would like to reverse that. He sees great opportunity to conserve resources and implement concepts of sustainable production in a practical and realistic manner, especially in the German machine building industry. “Extremely robust and durable machines have always been built in Germany,” says Köhler. “We can take advantage of this simply by utilizing an already available resource: used machines.” These machines are brought to the state of the art by Köhler and his team of over 20 employees, and are then able to go back into the production cycle.
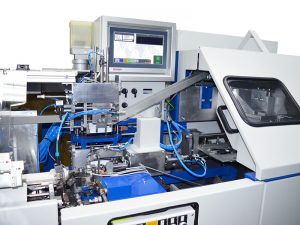
Along with machinery from the inventory of his second company, WOMA, an international second-hand machinery trader, Daniel Köhler works with machinery projects by contract. “Mostly, it is customer machines that come to us for a retrofit,” explains Köhler. He is responsible for the design and project planning in the company. Depending on how extensive the overhaul might be, even complete automation solutions are often designed and implemented. The heart of the WOMAtec Retrofit, however, is the new WOMAtec CNC control system. “Electronics are responsible for the limited life of the machines in most cases. The mechanics are still good, but the controls are defective and they are no longer reliable or the procurement of spare parts has become too difficult.” Owners of brush machines from the 1990s therefore face large investments in the near future. The WOMAtec CNC Retrofit is a cost-effective alternative. “Since the basic machine itself remains unchanged, existing mechanical spare parts continue to fit. And after a little bit of training in the new user interface, everything stays the same for the operator,” says Köhler.
The brush machine control specially developed by WOMAtec for up to five servo-controlled axes is based on components from Beckhoff and Festo. “This enables us to offer our customers long-term spare parts availability and the greatest possible independence in spare parts procurement. Nevertheless, we are of course available for spare parts supply and service,” Köhler says, referring to his highly qualified employees. In addition to programming and control cabinet construction, an entire mechanical overhaul is also carried out in-house. For a retrofit, the existing machine is disassembled “down to the last screw” and is completely rebuilt again. “We tell our customers, ‘Every screw is new,’ to make it clear that our overhaul isn’t just just a new paint job. After it’s been through our workshop, the machine is like new again,” Köhler explains.
In order to guarantee a high quality standard, all necessary work, starting with welding and sheet metal work, sandblasting and painting, up to the CNC-controlled production of new parts, is largely done in our own workshop. For this purpose, a recent investment in a new water jet cutting machine and a CNC machining center was made. “With our work, we breathe new life into old machines. We take the proven technology and give the owner an efficient and productive machine for another twenty years. For me, that’s sustainability in practice,” says Köhler.
A twenty-year-old fully automatic Zahoransky nail-brush machine before, during and after completion of the WOMAtec CNC retrofit.
Learn more about WOMAtec at www.womatec.com