ZAHORANSKY’s CUBE Redefines Production For Anchor-tufted Toothbrushes
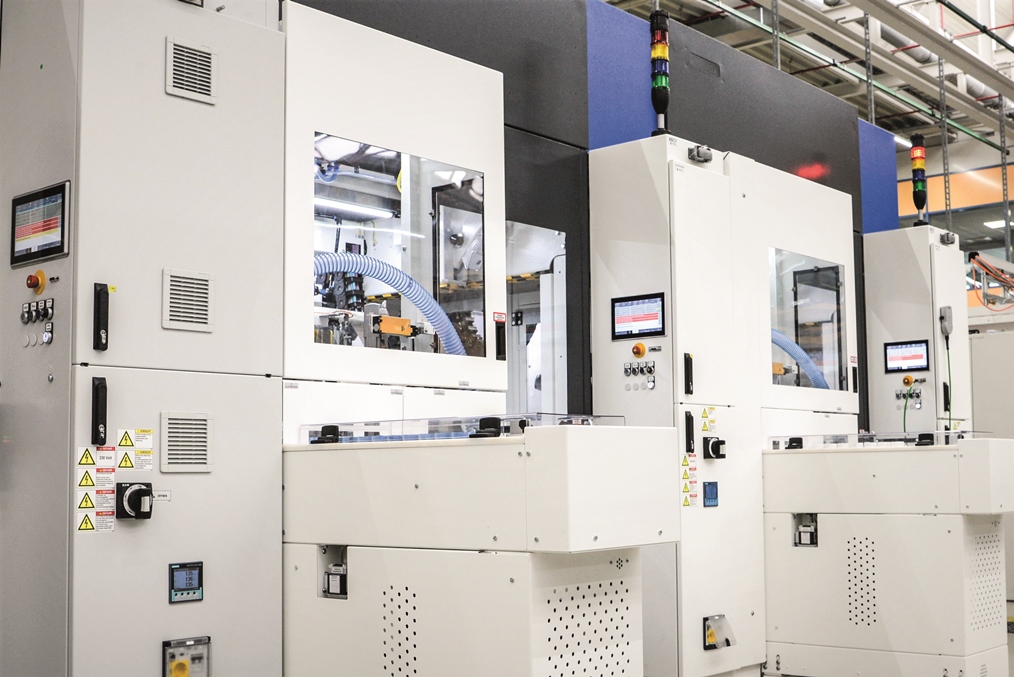
Revolution is a Square: ZAHORANSKY redefines the production of anchor-tufted toothbrushes with the CUBE
With its revolutionary CUBE, a machine for the production of anchor-tufted toothbrushes redesigned from the ground up, ZAHORANSKY clearly highlights its reputation as the leading full-service provider and partner of the brush industry. The CUBE offers scalable production with the utmost flexibility and highest level of quality thanks to a three-part modular construction, consisting of a base unit, supply unit and cover unit. Together with the ZMI retooled 4.0 machine controls, the machine can process both parallel as well as serial production tasks without making any changes to the mechanics. Various toothbrush models with different bundle designs can be produced on the same machine by simply loading the relevant program without any compromise in production quantity. The output with one CUBE Base Unit is 40 brushes per minute and quantities can be increased to 80 brushes by connecting a second CUBE Base Unit. Further gains are possible by adding additional modules. Robert Dous, Director of Sales & Marketing of ZAHORANSKY AG, explains, “With the modular design of CUBE, we have completely reinvented toothbrush production. This is how we live up to the expectations of our customers, who expect modern production environments geared towards maximum flexibility in terms of quantities and design.”
CUBE: maximum flexibility with the smallest footprint
The modular basic construction of the CUBE allows for toothbrush production with the utmost flexibility and efficiency while taking up minimal floor space. Additional base units can simply be integrated into an existing CUBE system for higher quantities or to adapt to new market demands placed on toothbrushes. The sequence of the tufting and finishing units can be adjusted. For example, with complex toothbrush trimming topographies (height/depth trimming), the lower filaments can first be tufted and trimmed before the upper filaments are processed, doing away with the complicated spreading process typically required. The CUBE is particularly flexible when it comes to processing: At higher quantities, it can run in parallel operation with all CUBES producing the same brush model. Serial operation can be activated for models with larger/smaller holes as well as deeper/higher bundles by simply loading the relevant program into the ZMI 4.0 controls. In addition to producing 40 brushes per minute per base unit, the previous tufting speed of 1,000 filaments/minute can also be improved to 1,200.
New feeding system for bulk material handles
In line with the new innovations, the machine boasts a redesigned feeding system for handles made of bulk material. It is scalable in terms of the required number of handles, similar to the CUBE itself. Optical camera recognition of the handle shapes ensures easy conversion to other models, and with it flexibility. The handles then run through the base unit – with units for tufting, trimming, and end rounding – through the carrier transport system (CTS) integrated into each CUBE. It is also possible to integrate additional devices for printing, quality assurance cameras, and so on. The finished toothbrushes are subsequently removed from the CUBE by a robot and placed on a transport line with the correct orientation. At the end of the line, the brushes are deposited into a tray for further processing or finishing in a packaging line, such as the Z.PACK.
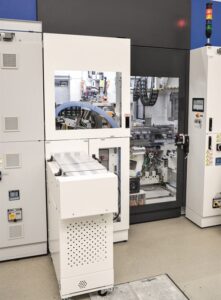
Delivered ready for use at a moment’s notice
With the CUBE, it’s not just what is on the inside that matters. ZAHORANSKY came up with a clever solution for delivery and installation at the customer’s facility: By moving the electronics and control cabinets up, the machine takes up less floor space. Every version of the CUBE can be delivered to the customer in a container, ready for use – no more lengthy assembly operations on site. The machine is up and running productively faster and takes up less space in the production hall. The machine has a transparent panel facing the operator, which additionally increases the efficiency of and accessibility for maintenance work.
ZMI 4.0: the smart machine controls
The Zahoransky Machine Intelligence (ZMI) 4.0 has been reprogrammed from the ground up, and is now even smarter and more closely aligned with the operator’s requirements. Intuitive touch controls with new icons and a wizard allow for operation of machines fitted to the new controls (currently CUBE, Z.SAILFIN, and Z.LYNX 3) without extra training. Programming takes place on the basis of pre-defined building blocks for certain motion sequences of the machine. For example, test users managed to program trimming profiles and start the machine five to ten minutes more quickly. ZMI 4.0 takes into account processes that logically follow each other, minimizing operating errors. If anything is unclear during operation or if questions arise, “Help me” wizards suggest suitable solutions. The integrated service mode makes it easier to request international support by overcoming language barriers with a unique ID number stored in every field of the display — for example in the settings of the filament feed. Only the ID needs to be mentioned when making an inquiry, for easier identification of errors while speeding up the support process.
Learn more at www.zahoransky.com.